IBSim in R&D
IBSim is already being used within R&D cycles to accelerate development by providing additional insight at each stage.
The progress along the research and development (R&D) cycle of producing a new concept is described by its ‘technology readiness level‘ (TRL), which is a method of categorising its maturity stage. These levels range from the conceptual stage (TRL 1) to full production with a proven in-service track record (TRL 9).
To increase efficiency in R&D cycles it is desirable to accelerate progress through the TRLs. Within manufacturing, identifying optimal products (their design, material selection, usage parameters etc.) is achieved by iteratively down-selecting candidates through testing.
Initially, there are likely to be a large number of candidates which are tested with representative sub-samples due to cost and time considerations. Through the R&D cycles, as the number of candidates decrease, the complexity of the part and testing increases from small coupons to sub-components up to full scale assemblies.
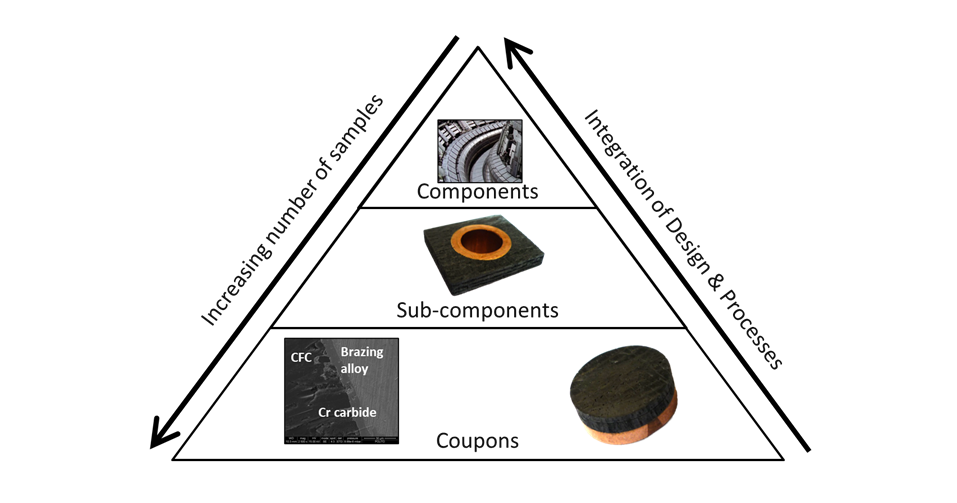
Much of this development process is constrained by available resources. That is, the number of candidates which may be considered are limited by costs and time. Virtual testing through computational simulation techniques have increasingly been facilitating the R&D process. With simulations it is possible to iterate through many more designs quickly and cheaply without needing to prototype concepts.
However, there exists a gap between in observations during simulation and experiments. As such, simulations are used as first stage guidance but there is still a heavy reliance on experimental testing during R&D. Improved accuracy in simulations will lead to more rapid R&D development.
Image-based simulation (IBSim) is an approach that closes this gap between simulation and experiment. By digitising a real prototype, micro-scale accurate simulations can be carried out on the part ‘as manufactured’ rather than ‘as designed’. This means its geometry is no longer idealised and simulations account for impact on performance due to manufacturing processes by inherently including features such as deviations from tolerance and micro-porosity.
Within R&D, IBSim allows one manufactured prototype to be tested to destruction multiple times by using a virtual representation of the manufactured part which is faithful on the micro-scale. In addition to replicating laboratory testing through simulation, it is possible to extrapolate to scenarios more representative of real-world conditions e.g. increased number of cycles, real loading rates and values, complex loading with multiple mechanisms. This is because IBSim testing is not constrained by the limitations of the laboratory. That means much more valuable data can be obtained from a single prototype, significantly reducing costs.
Through being able to directly compare results from experimental and simulation results, IBSim benefits from verified results with increased confidence values compared with simulations using idealised geometries. This is invaluable within the industrial sector when simulating conditions outside what can be tested in the lab.
IBSim in materials development
IBSim can be used in materials development to perform virtual characterisation to reduce the number of physical tests and thus the volume of material required.
The process of manufacturing novel materials can often be a rapid process which only requires the variation of some parameters during fabrication. This can create different microstructures which leads to different material properties. However, the process for characterising the new properties of the material can involve a significant effort and thus cost. If it is desired to measure a range of properties, this can require fabrication of many samples for a series of experimental tests. And, because the fabrication method is likely to be immature during the R&D phase, there will likely be non-negligible variation between the series of samples.
By using IBSim, it is possible to perform virtual testing with a suite of simulations that emulate laboratory material characterisation from one manufactured block of material that’s digitally ‘cut’ to the required dimensions. This way, new materials can be more rapidly characterised to identify the strongest candidates.
Because of the digitisation process from a real material, IBSim can be used for simulations of extremely complex geometries such as fibre composites or foams with no need for idealisation. Additionally, it is possible to digitally alter the structure to see what impact this has on the properties. For example, the volume of pores or the thickness of foam ligaments could be increased/decreased to investigate the benefits of imposing additional control on the material processing.

IBSim in NDT/NDE as QA
The full power of IBSim lies in part-specific simulations for all components manufactured in a production line to give accurate individual performance analyses.
The full potential of IBSim has not yet been realised and its use thus far has predominantly been within the academic sector or with small scale use for R&D in the industrial sector. With recent advancements in volumetric imaging (e.g. micro XCT) and computational hardware it is now feasible to include IBSim as a production line tool.
IBSim is best suited to scenarios where there exists a non-negligible degree of variation from between the finalised component and initial design, or from one component to another within a batch, such as:
- Additive manufacturing (or 3D printing)
- Fibre composites
- Joining or bonding zones
Used as a non-destructive evaluation test (NDE / NDT), it can be used for virtual quality assurance (QA) on each part once completed. Because IBSim uses non-idealised geometries, it will generate part-specific performance analyses. For some production lines, this means moving past pass/fail testing to a performance grading of components. This enables suppliers to supply appropriately to the desired application rather than supply over engineered components, this is akin to supply of materials which are graded according to purity. This offers substantial efficiency gains and, thus, cost savings through the reduction of scrapped parts.
In an assembly of similar parts, IBSim may be used to identify the optimal configuration e.g. by avoiding locating two lower performing units in proximity to each other.
Furthermore, with IBSim, each part has a ‘digital twin’ which can be used to simulate in-service use for improved accuracy in determining maintenance windows or when the component’s end of life is reached. This digital asset can be supplied to the customer or retained by the manufacturer and performed as an added value service.

Industrial usage of IBSim
The increasingly widespread availability of industrial micro XCT scanners and continuously increasing computing power means that meaningful deployment of IBSim technology in the industrial sector is now possible.
Simulation tools such as FEA have been standard practice within the design cycle of the industrial sector for many years. The industrial micro XCT market has seen a steady growth of 10% pa. in recent years. Despite this, IBSim is not yet widely used in industry. This is likely due to some of the perceived additional challenges associated with preparing volumetric image data for IBSim which can be a barrier to industrial scale up if not addressed correctly.
The research focus of the IBSim group is to address barriers to adoption of IBSim by the industrial sector through developing tools and methodologies for scale-up.
Due to the decreasing cost of computing and increasing availability of industrial micro XCT scanners, IBSim is becoming increasingly accessible to small and medium sized enterprises (SMEs). We have demonstrated that the hardware requirements of performing IBSim is well within the capability range of a modest computing cluster affordable to a medium sized enterprise, costing of the same order as an industrial micro XCT scanner. Alternatively, with the widespread adoption of cloud computing and availability of ‘CT as a service’, this would serve as a flexible avenue for smaller sized enterprises not in the position to outlay the capital expenditure the required hardware.
To assist users to learn more about how to implement IBSim in their workflow the IBSim group regularly organises training courses which are open to both academia and industry. Keep an eye out on our events page for upcoming courses. In future, the aim is to offer these as online courses. In the meantime, some of this material is available online on our past events pages. Alternatively, if you’re interested in working with us to develop a customised solution for your needs, please contact us directly.